Modular Conveyors Forefront Of Kaizen Activity, Giving Automotive Suppliers an Economic Advantage In Transitioning Market
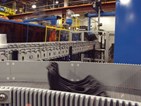
Forward thinking automotive suppliers know that change is the benchmark in the automotive industry. However, on the heels of an oil crisis, Global economic slowdown and heated Congressional debates about the fate of US automakers, suppliers are under unprecedented pressure to take a more rigorous approach to productivity improvement that allows them to quickly adapt to changing market conditions.
With building-block versatility, modular conveyor systems are one of the few remaining frontiers of productivity improvement that complements the Kaizen philosophy of continuous improvement.
"Modular conveyors give us unlimited opportunities and keeps us from having obsolete equipment with fixed length conveyors," says J. C. Noll, Senior Production Engineer at North American Lighting Inc's (NAL) Flora, IL plant. "Fixed conveyors just back you into a corner. If you want to improve a process or work on some Kaizen activity you are somewhat strapped to the fixed length conveyor's length unless you want to go through the pain of cutting it down and then getting a new belt configured for that."
NAL has been manufacturing lighting products, from concept to product launch, for vehicle manufacturers such as Toyota, GM, Honda, Nissan and Subaru as well as several other manufacturers. The Flora, IL plant produces headlamps, fog lamps and auxiliary combination systems.
NAL's manufacturing process is based on the Koito Production System (KPS), which ensures that costs are closely controlled; inventories are held to a minimum, engineering changes are implemented quickly and deliveries are on time.
Noll says that NAL is always looking for ways to improve its processes and look toward the big four: cost, delivery, timing and quality.
Modular conveyor systems offer a sustainable, eco-friendly equipment solution providing lower total cost of ownership savings in many areas including, energy savings, reduced maintenance costs, shipping, installation, and most notably in reconfiguration.
"If we purchased 5 new conveyors which were all fixed length and a year and a half from now we wanted to make some other improvement those conveyors might not have an application at that point and they would become obsolete or idle equipment and then force additional expenditure," explains Noll.
"With the DynaCon modular conveyor if we want to make a change to this layout, we buy three additional modules and expand the conveyors three feet because now we can make it work," he says.
The modular conveyor system is manufactured by Muskegon, MI-based Dynamic Conveyor and is easily reconfigured by removing, inserting or exchanging modules that are available in lengths as short as 6."
The Flora NAL plant uses the modular conveyor system 24/5 to move product from one of their 28 hydraulic and electric thermoplastic molding machines, ranging from 90-1450 tons, where the product is robotically placed on the conveyor, sent to an operator for inspection and then packaged or conveyed to another area for a secondary application.
Like many other suppliers in the automotive industry, NAL manufactures products with varying spans of production ranging from 18 to 60 months and therefore need to reconfigure often.
"The flexibility of being able to change work cell layouts is the bonus," Noll says. "With the modular system you can add or subtract modules to reconfigure based on Kaizen activity when making productivity improvements or streamlining operator utilization."
At NAL, Kaizen activity is a daily activity and that is where the flexibility of a modular system is a big advantage. Noll says, "we can move quickly to adapt a new idea."
"It goes back to fixed length conveyors and when you make those changes, they become obsolete and that has always been a frustration of mine. Trying to come up with the storage space to store a 24-foot conveyor that is no longer applicable becomes a problem. Floor space is a premium in our business and external storage has a cost," says Noll.
Not only does it cost to store it, but that piece of equipment's time of service is cut down as well when it is stored outside in a shelter.
The use of modular conveyor systems also eliminates the need for transition points. If a curved application is necessary, the curved module is one piece from start to end with a modular system, whereas, a fixed length conveyor may take three pieces with a transition point.
"Based on the cosmetic requirements of our product, a fixed conveyor might increase our defect ratio. So the capability of doing a curve within the same conveyor adds a lot of flexibility for us," says Noll.
The use of modular conveyors with a selection of components and accessories enables manufacturers to adapt to a variety of challenging situations, such as running the conveyor around obstacles, transporting parts underwater, walk-under configurations, suspending the conveyor from ceilings and even continuing production flow to or from fixed metal systems.
The conveyors are manufactured of impact-resistant polycarbonate panels that are durable, and can be replaced easily if damage occurs. There is no need to scrap the entire conveyor -- just those modules that need replacing. The system utilizes plastic link style belting, so if there is damage to the belt, then replacement of only the damaged piece is necessary.
Another advantage of the modularity of the system, according to Noll, is the ability to share equipment between the facilities. The Flora, IL facility was the first to employ the DynaCon system, but over the past six years, as well as expanding the number of conveyors in that facility, some of NAL's other facilities have implemented the modular conveyor system.
"We have a sister forward lighting plant in Paris, and rear lighting in Salem as well as our new plant in Alabama. We can share that equipment between the plants and it makes it much better for us," Noll says. "If I needed a module, I can just call my fellow engineers in the other facilities and find out if they have any inventory."
"From an engineer's standpoint it's easy to reconfigure. You can do more on your own with DynaCon. And the programmability of the modular system and how it interfaces with auxiliary equipment, robotics, etc. is impressive," he says.
Fixed metal conveyors may require expensive, specialized engineering as well as costly, time-consuming installation techniques, such as cutting and welding. These modular systems offer robust features while eliminating special engineering and installation requirements. Two workers can easily assemble most modular conveyors in less than one hour. An animation that demonstrates the ease of reconfiguring the system can be accessed at http://www.dynamicconveyor.com/downloads/conveyor_flash/reconfigurability.wmv.
Noll says, "the system is also easier to bring into the plant because it is so compact." DynaCon modular conveyors ship partially assembled in a box, taking minimal space on the delivery truck. While standard conveyors ship fully assembled, require special crating and take more space in a delivery truck, resulting in increased costs for delivery of the conveyor as well as maneuvering challenges getting them into the facility.
Beyond the cost savings that repurposing the conveyors bring, and reduced shipping and installation costs, Noll says, "no maintenance is needed with this modular conveyor system." Most standard conveyors require lubrication, either due to continuous usage or after cleanups with water. The modular conveyors are self-lubricating.
In addition, many fixed conveyor systems and even one-off designs have a short limited warranty period which appear on the front end to save on purchase price, but is often a dangerous gamble, especially when an expired warranty affects service response.
DynaCon systems carry a five-year warranty on conveyor materials and workmanship as well as a warranty on the belts, motor and other electric components.
Belting on traditional conveyors is time-consuming to service and requires frequent realignment, regular lubrication and continuous belt tensioning. However, the link style belts on most modular conveyors are maintenance free. When modular link-style belts are damaged, replacement of only the damaged section of the belt is necessary.
Based on each application, the company's modular conveyors utilize the most energy efficient motors, which range from 1/30 HP to 1 HP, and cost just pennies a day to operate. Specifying the right energy efficient motor for each application and easily exchanging it when torque requirements change keep kilowatt usage to a minimum. Lowering the kilowatts used not only saves money, but also reduces carbon emissions during the making of electricity. Savings can be seen with electric power consumption all day long, year after year. Companies that will endure through this global economic crisis are those like NAL, Inc. that employ equipment solutions that allow for continuous improvement, offer flexibility and lower total cost of ownership.
For more information visit http://www.dynamicconveyor.com/whydynacon or www.dynamicconveyor.com.
SOURCE: North American Lighting Inc.