Metris K-Series Qualifies RCR Chassis For NASCAR Victory
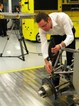
To cut seconds off lap times, RCR engineers use Metris metrology equipment to optimize and tune the chassis/suspension performance of their premium race vehicles. Metris K-Series allows a complete chassis build to be referenced from a single common coordinate system, increasing data capture efficiency with over 40%. Higher metrology performance, precision and repeatability secure NASCAR chassis certification and strengthen RCR chassis engineering and manufacturing expertise. In addition, RCR recently opted for Metris MMD laser scanning to capitalize on fast, accurate and non-contact digitization of suspension components to drive FEA and CFD vehicle simulation.
Facing tighter structural and dimensional NASCAR requirements
"The recent introduction of the Car of Tomorrow (COT) concept represents the biggest change in NASCAR race vehicle regulation in the last 20 years," says Chris Hussey, Director of Engineering. "COT further tightens overall NASCAR race car requirements and forced racing teams to re-think their vehicle engineering processes. This basically means that all teams start off from scratch with COT when developing next-generation race cars for the 2008 NASCAR Homestead season and servicing them all season. In terms of chassis/suspension engineering, geometric inspection and verification plays a key role throughout the entire development process. Our choice for Metris K-Series' fast and accurate metrology capability enables us to reduce time spending for routine measurement and free up surplus engineering time."
Chris Hussey and his team are responsible for RCR chassis/suspension engineering and production. "When verifying NASCAR-mandated body and suspension points, Metris K-Series assists us in efficiently acquiring high-precision geometric data," Chris Hussey explains. "And beyond certification, we use the same equipment to acquire RCR-determined critical performance points to engineer as much competitive edge as we can in getting a potential winner at the start grid." All it takes to set up the system is to position its optical CMM (Coordinate Measuring Machine) next to the vehicle and immediately start measuring using the handheld SpaceProbe. The linear CCD cameras built into the system's optical CMM module apply triangulation to accurately track the tip position of the SpaceProbe. Among NASCAR mandated chassis characteristics are tube thickness, tube locator points as well as the rigidity and torsional stiffness of the chassis frame. For the suspension section, NASCAR-specific verification testing focuses on upper/lower controller arms and spindle drop/offset values in addition to camber, toe and other suspension-specific characteristics.
Introducing metrology with higher measurement turnaround
"As the working volume of the Metris system easily fits an entire RCR chassis, Metris K-Series allows all measurement points to be measured in one go using a single coordinate system, eliminating leap frogging altogether," Chris Hussey explains. "Where final verification of an entire chassis assembly previously took almost an entire day, a single RCR engineer now completes the same metrology job over 40% faster!" In the past, RCR performed this kind of measurement using an articulated arm based measurement setup. The limited reach of the arm required multiple setup positions around the vehicle, which in many cases kept two operators busy and ultimately delivered inaccurate and/or inconsistent data due to potential misalignment.
While tight regulation applies to most parts of the vehicle chassis, the suspension system represents a relatively unrestricted zone that leaves plenty of opportunity to engineer inherently faster race cars. After establishing subtle compromises between vehicle aerodynamics and handling performance, detailed suspension design and tuning begins. Chris Hussey explains that consistent tire patch contact with the track can be maintained under all racing circumstances, by adapting suspension characteristics to align the driving behavior of the car to the size and banking of the oval track. "Besides focusing on designing for lighter vehicle weight, we modify the suspension design, all within the design boundaries imposed by NASCAR. We tune caster and camber in the asymmetric suspension along with toe, and design the right amount of toe out that can be gained on the inside tire in a turn. Following our strategy to bringing more engineering in-house, we take full control over chassis/suspension engineering and safeguard our technical expertise."
Better engineering decisions by narrowing down technical options
Lessons learned from acquiring more in-depth engineering information support RCR engineers in developing chassis design innovations that step up race chassis performance. Chris Hussey says that in the limited time frame in between races and in the off-season, accurate and repeatable metrology helps quickly narrow down technical options and make the right engineering choices. "Accurate, consistent and repeatable data ultimately makes RCR's yearly production of 40-50 chassis/suspension builds truly identical. This is essential in building the capability to compare engineering information, irrespective of the chassis/suspension unit being considered. We insert all acquired 3D measurement information into our company-wide engineering knowledge base, to strengthen our capability to understand the complex physics that are involved in top-level NASCAR racing."
The hectic pace of a NASCAR racing season calls for fast action, especially when considering post race and damage analysis. Hussey indicates that due to the frantic NASCAR race schedule, he only has Mondays through Thursdays to deliver race-ready vehicles. "As soon as race cars become available after a race, our engineers use Metris K-Series to assess torsional twisting of the vehicle chassis and run other specific tests. We noticed that accurate and predictable measurement results show clear trends in terms of mechanical vehicle wear and collision damage. This enables us to promptly define countermeasures and complete repair in time. Fast and in-depth investigation avoids trial-and-error analysis and reduces the turnaround for similar chassis/suspension builds in the future."
Evolving from measurement equipment to engineering aid
RCR clearly sees premium metrology solutions more as engineering aid than measurement equipment. In this regard, RCR recently extended its metrology capability with Metris MMD, a powerful non-contact laser scanning solution. Featuring a wide laser stripe and all-digital operation, the arm-mounted MMD allows complete detailed geometric scans of small to large vehicle body parts to be captured in record time. Scanning at a rate of multiple thousands points per second creates a detailed digital 3D copy of the scanned surface, which easily adds up to millions of measurement points. RCR uses the Metris MMD to reverse engineer chassis/suspension to quickly create virtual FEA and CFD component and assembly models. These digital models are leveraged to run simulations in different engineering fields, including dynamic motion, durability and aerodynamics.
Major breakthroughs in manufacturing capabilities are generally preceded by major breakthroughs in metrology. "Metris brought us dimensional accuracy and manufacturing consistency that clearly exceeds NASCAR Car of Tomorrow certification requirements," Chris Hussey concluded. "More importantly, Metris metrology helps us lay bare the root causes of race car limitations, which enables us to create that extra competitive advantage that separates winners from the pack."
SOURCE: Metris